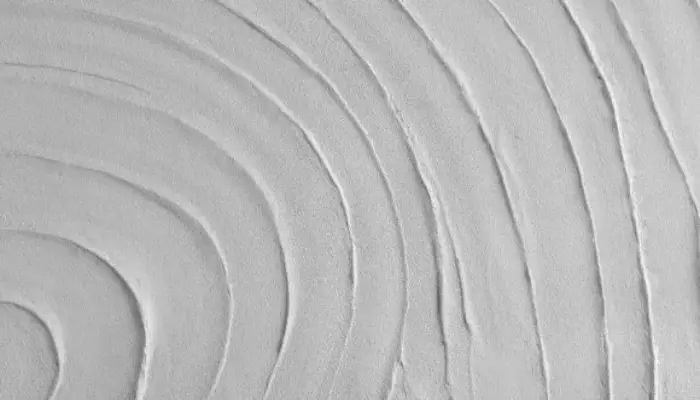
L'antidispersione è un importante indicatore tecnico per misurare la qualità dell'antidisperso. L'idrossipropilmetilcellulosa (HPMC) è un composto polimerico idrosolubile, conosciuto anche come resina idrosolubile o polimero idrosolubile. Aumenta la consistenza della miscela aumentando la viscosità dell'acqua di impasto. È un materiale polimerico idrofilo. Può essere disciolto in acqua per formare una soluzione o una dispersione. Gli esperimenti dimostrano che quando la quantità di superfluidificante a base di naftalina aumenta, l'aggiunta di un agente di riduzione dell'acqua riduce la resistenza alla dispersione della malta cementizia appena preparata. Questo perché il superfluidificante a base di naftalene è un tensioattivo.
Quando il superfluidificante viene aggiunto alla malta, si dispone direzionalmente sulla superficie delle particelle di cemento in modo che la superficie delle particelle di cemento abbia la stessa carica elettrica. Questa repulsione elettrica costringe a smontare la struttura di flocculazione formata dalle particelle di cemento e a rilasciare l'acqua avvolta nella struttura, causando la perdita di una parte del cemento. Allo stesso tempo, è emerso che con l'aumento del contenuto di HPMC, la resistenza alla dispersione della malta cementizia appena preparata può migliorare sempre di più.
1. La dispersione di HPMC verso le caratteristiche di resistenza della malta
L'additivo per calcestruzzo non disperdibile a base di idrossipropilmetilcellulosa (HPMC) subacquea viene applicato nella progettazione delle fondamenta del ponte della superstrada e il grado di resistenza di progetto è C25.
Secondo gli esperimenti di base, il dosaggio del cemento è di 400 kg, il composto miscelato con fumo di silice è di 25 kg/m3Il dosaggio ottimale di HPMC è pari a 0,6% del dosaggio di cemento, il rapporto acqua-cemento è pari a 0,42, il rapporto sabbia è pari a 40%, e il dosaggio di superfluidificante a base di naftalene è 8% del dosaggio di cemento, il provino di calcestruzzo all'aria è di 28 giorni, il valore medio di resistenza è di 42,6MPa, il calcestruzzo preparato sott'acqua a un'altezza di caduta di 60 mm è di 28 giorni, il valore medio di resistenza è di 36,4MPa, il rapporto di resistenza del calcestruzzo formato in acqua rispetto a quello formato all'aria è di 84,8%, l'effetto è comparabilmente più evidente.
1. L'aggiunta di HPMC ha un significativo effetto ritardante sulla miscela di malta. Con l'aumento del contenuto di HPMC, il tempo di presa della malta si allunga progressivamente. A parità di contenuto di HPMC, il tempo di presa della malta formata sott'acqua è più lungo di quello della malta formata in aria. Questa caratteristica è vantaggiosa per il pompaggio del calcestruzzo sott'acqua.
2. La malta cementizia appena preparata, miscelata con idrossipropilmetilcellulosa ha buone proprietà coesive. Non ha quasi alcun sanguinamento.
3. La quantità di idrossipropilmetilcellulosa (HPMC) e il fabbisogno idrico della malta mostrano che la quantità di acqua è stata ridotta. prima una diminuzione e poi un aumento significativo.
4. L'aggiunta di un agente di riduzione dell'acqua migliora il problema dell'aumento del fabbisogno idrico della malta.ma la sua quantità di miscelazione deve essere controllata in modo ragionevole, altrimenti la resistenza alla dispersione subacquea della malta cementizia appena preparata sarà talvolta ridotta.
5. La differenza di struttura tra il campione di malta di cemento miscelato con HPMC e il campione di malta di cemento vuoto è minima. I campioni di malta cementizia colati in acqua e all'aria presentano poche differenze in termini di struttura e densità. Il provino di malta cementizia di 28d formato in acqua è leggermente allentato. Il motivo principale è che l'aggiunta di HPMC riduce notevolmente la perdita e la dispersione del cemento versato in acqua, ma allo stesso tempo riduce anche la densità dell'impasto composto da cemento e pietre. In un progetto, pur garantendo l'effetto di non dispersione in acqua, la quantità di HPMC deve essere ridotta al minimo.
6. Aggiungendo idrossipropilmetilcellulosa (HPMC) in acqua all'additivo per calcestruzzo non disperdibile e controllando il dosaggio è utile per la forza. Il progetto pilota dimostra che il rapporto di resistenza del calcestruzzo formato in acqua rispetto a quello formato in aria è di 84,8%, l'effetto è comparabilmente più evidente.
PRODOTTO MIKEM PER MALTE A BASE DI CEMENTO
Come additivi ad alte prestazioni progettati per malte specialiI nostri prodotti a base di etere di cellulosa MelaColl™ e Mikrant RDP sono ampiamente utilizzati nelle malte cementizie e possono rafforzare significativamente le proprietà e le prestazioni delle malte a base di cemento nei seguenti modi:
- Migliorare l'adesione
- Migliora la lavorabilità e la consistenza
- Migliorare la ritenzione idrica
- Accelerare l'ingresso dell'aria e aumentare la lubrificazione
- Migliorare l'idrofobicità
- Aumentare la durata
Se cercate un prodotto eccellente a base di idrossipropilmetilcellulosa (HPMC) per le malte a base di cemento, non esitate a CONTATTO per maggiori informazioni sui prodotti o per un campione! Siamo sempre pronti a rispondervi con un servizio personalizzato e una formula su misura!
Lascia una risposta