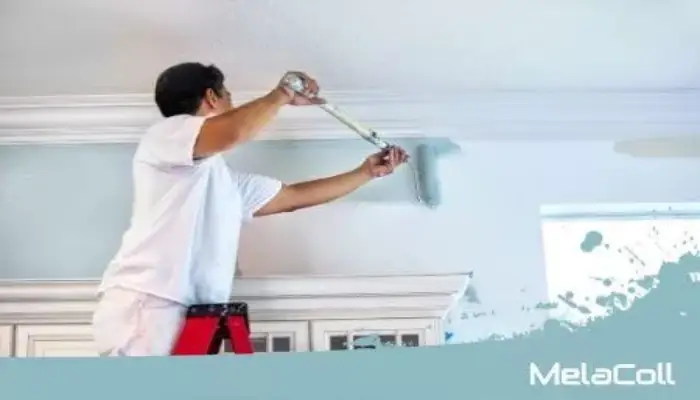
La celulosa es un compuesto polimérico natural de macromoléculas polisacáridas, y su estructura química se basa en la β-glucosa anhidra. Cada anillo base tiene un grupo hidroxilo primario y dos grupos hidroxilo secundarios. Se puede obtener una serie de derivados de la celulosa mediante modificación química, como por ejemplo éter de celulosa. Los éteres de celulosa se utilizan ampliamente en muchas industrias, y el éter de celulosa en la industria de revestimientos es uno de los principales ámbitos de aplicación de los éteres de celulosa.
1. Propiedades del éter de celulosa
1.1 Aspecto
El éter de celulosa es un polvo fibroso fluido de color blanco o blanco lechoso, inodoro, no tóxico, fácil de absorber la humedad y que se disuelve en agua formando un coloide viscoso transparente y estable.
1.2 Solubilidad
MC es soluble en agua fría, insoluble en agua caliente y soluble en algunos disolventes; MHEC es soluble en agua fría pero insoluble en agua caliente y disolventes orgánicos. Solubilidad de HPMC Sin embargo, MC y MHEC precipitarán cuando se caliente la solución acuosa de MC y MHEC. El MC precipita a 45~60℃, mientras que la temperatura de precipitación del MHEC eterificado mixto aumenta a 65~80℃.
1.3 Expansión retardada
El éter de celulosa tiene un cierto grado de hinchamiento retardado en agua de pH neutro, pero puede superar este hinchamiento retardado en agua de pH alcalino.
1,4 Viscosidad
El éter de celulosa se disuelve en agua en forma coloidal, y su viscosidad depende del grado de polimerización del éter de celulosa. La solución contiene macromoléculas hidratadas. Debido al entrelazamiento de las macromoléculas, el comportamiento de flujo de la solución es diferente al del fluido newtoniano, pero muestra un comportamiento que cambia con la fuerza de cizallamiento. Debido a la estructura macromolecular del éter de celulosa, la viscosidad de la solución aumenta rápidamente con el aumento de la concentración y disminuye rápidamente con el aumento de la temperatura.
1.5 Estabilidad biológica
El éter de celulosa se utiliza en la fase acuosa. Mientras haya agua, las bacterias crecerán. El crecimiento de las bacterias conduce a la producción de bacterias enzimáticas. Las bacterias enzimáticas rompen el enlace de la unidad de anhidroglucosa no sustituida adyacente del éter de celulosa, lo que reduce el peso molecular del polímero. Por lo tanto, si la solución acuosa de éter de celulosa se va a almacenar durante mucho tiempo, es necesario añadir conservantes. Esto es cierto incluso cuando se utiliza éter de celulosa antibacteriano.
2. Aplicación de éter de celulosa en el revestimiento
Éter de celulosa en el revestimiento, como HPMCHEC desempeña un papel importante. La adición de 0,2% a 0,5% de la fórmula total puede espesar, retener agua, evitar la precipitación de pigmentos y cargas, y aumentar la adherencia y la fuerza de unión.
2.1 Viscosidad
Sobre el grado de viscosidad del éter de celulosa para revestimientos, puede ver el siguiente vídeo:
La viscosidad de la solución acuosa de éter de celulosa cambia con la fuerza de cizallamiento. Los recubrimientos y lechadas espesados con éter de celulosa también presentan esta característica. Para que el revestimiento sea fácil de aplicar, hay que seleccionar cuidadosamente el tipo y la cantidad de éter de celulosa. En el caso de los revestimientos, cuando se utiliza éter de celulosa, productos de viscosidad media se puede utilizar.
2.2 Retención de agua
El éter de celulosa puede impedir que la humedad penetre rápidamente en el sustrato poroso, de modo que durante todo el proceso de construcción puede formar un revestimiento uniforme sin hacer que se seque demasiado rápido. Cuando el contenido de emulsión es alto, el requisito de retención de agua puede cumplirse utilizando menos éter de celulosa. La retención de agua de revestimientos y lechadas depende de la concentración de éter de celulosa y de la temperatura del sustrato de revestimiento.
2.3 Estabilizar pigmentos y cargas
Los pigmentos y las cargas tienen tendencia a precipitar. Para mantener el revestimiento uniforme y estable, el pigmento de relleno debe estar en suspensión. El éter de celulosa en el revestimiento puede hacer que éste tenga una viscosidad específica y no produzca precipitación durante el almacenamiento.
2.4 Adherencia y fuerza de unión
Debido a la excelente retención de agua y adherencia del éter de celulosa, se puede garantizar una buena adherencia entre el revestimiento y el sustrato. El MHEC y el NaCMC tienen una excelente adherencia y adhesión en seco, por lo que son especialmente adecuados para la pasta reforzada con papel, mientras que el HEC no es adecuado para este fin.
2.5 Función coloide protectora
Debido a la hidrofilia del éter de celulosa, puede utilizarse como coloide protector para revestimientos.
2.6 Espesante
El éter de celulosa se utiliza ampliamente en la pintura de látex como espesante para ajustar la viscosidad de construcción. Hidroxietilcelulosa de viscosidad media y alta y la metilhidroxietilcelulosa se utilizan principalmente en pinturas en emulsión. A veces, el éter de celulosa puede utilizarse junto con espesantes sintéticos (como poliacrilato, poliuretano, etc.) para mejorar las propiedades específicas de la pintura de látex y dar a la pintura de látex una estabilidad uniforme.
3. En resumen
Los éteres de celulosa tienen excelentes propiedades de retención de agua y espesantes, pero algunas propiedades y aplicaciones son diferentes. Tenemos que elegir grados de viscosidad según las diferentes aplicaciones. Los éteres de celulosa aniónica forman fácilmente sales insolubles en agua con cationes divalentes y trivalentes. Por lo tanto, en comparación con la metilhidroxietilcelulosa (HEMC) y la hidroxietilcelulosa (HEC), la carboximetilcelulosa sódica tiene menor resistencia a la maceración. Pero HPMC y CMC también tienen muchas diferencias, debe elegir según su aplicación.
Dejar una respuesta