
Tile adhesive is an adhesive used for pasting ceramic tiles, stone, and other building materials, whose quality is directly related to the paving effect and the durability of the construction. In recent years, Redispersible Polymer Powder (RDP) has become an important additive in tile adhesives due to its unique chemical and physical properties. The addition of RDP can not only enhance the bonding strength of tile adhesive but also improve its flexibility, water resistance, and crack resistance. This article will deeply explore the specific application effects, influencing factors, and matters needing attention when using RDP in tile adhesives.
Application Effects of RDP in Tile Adhesive
Improvement of bonding strength
As a polymer additive, RDP can form a uniform polymer film in tile adhesive through its dispersibility in water. The existence of this film makes the tile adhesive have higher bonding strength after drying, which can effectively stick the tiles and ensure that they do not easily fall off during long-term use. Especially when used in humid environments or outdoors, the viscosity-increasing effect of RDP is particularly obvious.
Enhanced flexibility and crack resistance
During the laying process of tile tiles, the substrate may undergo slight deformation due to temperature changes, humidity fluctuations, or external forces. If the tile adhesive lacks sufficient flexibility, it may cause cracks between the tile and the substrate, affecting the overall aesthetics and service life. RDP can significantly improve the flexibility and crack resistance of tile adhesive by forming flexible polymer chains during the drying process, thereby maintaining a good bonding state under external forces.
Improvement of water resistance and freeze-thaw resistance
For tile adhesives that need to be used in humid or cold environments, water resistance and freeze-thaw resistance are crucial performance indicators. The addition of RDP can improve the water-resistance of tile adhesive, allowing it to maintain good bonding performance even if it is exposed to moisture for a long time. At the same time, RDP can also enhance the freeze-thaw resistance of tile adhesive to prevent damage caused by freeze-thaw cycles when the temperature changes rapidly.
Factors Affecting the Effectiveness of RDP Use
Adding the amount of RDP
The amount of RDP added directly affects the final performance of the tile adhesive. Usually, the additional amount of RDP is between 1-5%, which is adjusted according to different application scenarios and base materials. Adding too little may not give full play to the viscosity-increasing and flexible effects of RDP; adding too much may increase the cost of the tile adhesive, and in some cases may lead to changes in the rheological properties of the adhesive.
Type and treatment of the substrate
The type of base material and surface treatment have a significant impact on the performance of RDP in tile adhesives. For example, the concrete base has strong water absorption, which may affect the redispersion effect of RDP in water, thereby affecting its distribution and role in tile adhesive. Therefore, before using RDP-enhanced tile adhesive, you should ensure that the substrate surface is clean and flat, and if necessary, interface treatment can be performed to improve the bonding effect.
Construction environmental conditions
Environmental conditions such as temperature and humidity are also important factors that affect the effectiveness of RDP. In a high-temperature or low-humidity environment, the water in the tile adhesive evaporates quickly, which may prevent the RDP from being fully dispersed, thus affecting its effectiveness. On the contrary, in low-temperature and high-humidity environments, the drying speed of tile adhesive is slowed down and the curing time may need to be extended. Construction personnel should adjust the construction process according to specific environmental conditions to ensure that the tile adhesive can fully exert its performance.
Interactions with other additives
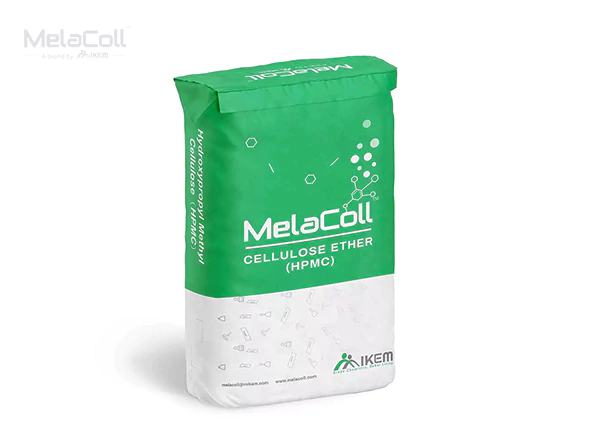
Melacoll® HPMC can significantly enhance the water retention of the putty.
Cellulose ethers (such as HPMC), fillers, and other additives are usually added to tile adhesives. The interaction between these additives and RDP will also affect the final bonding effect. For example, the addition of HPMC can improve the water retention of tile adhesive and extend the operating time, but if excessive addition is made, it may affect the dispersion and bonding effect of RDP. Therefore, when designing formulas, the interaction of each component should be comprehensively considered and the proportions should be optimized.
Precautions When Using RDP
Formulation design
When using RDP, formulation design should be tailored to specific application needs. For example, for tile adhesives that require higher flexibility, the amount of RDP added can be appropriately increased; for applications where water resistance is the main requirement, RDP products with higher hydrophobicity can be selected. At the same time, attention should also be paid to the quality differences between different production batches to ensure the stability of the formula.
Storage and transportation
RDP is sensitive to environmental conditions, particularly high temperature and humidity, which can cause it to absorb moisture and agglomerate, thereby impacting its effectiveness. To maintain its quality, RDP should be stored in a dry, well-ventilated environment and kept away from direct moisture exposure. During transportation, it's important to avoid prolonged exposure to direct sunlight or high temperatures.
Construction specifications
During the construction process, construction specifications should be strictly followed, especially in base treatment and tile adhesive preparation. The substrate should be kept clean, dry, and free of loose old glue or other impurities. The tile adhesive should be used as soon as possible after preparation to prevent performance degradation caused by being left for too long. In addition, construction workers should wear appropriate personal protective equipment to avoid inhaling dust or contact with skin.
Quality inspection and control
To ensure the final use effect of the tile adhesive, quality testing should be carried out before construction, especially the quality of the RDP, the bonding strength, flexibility, and water resistance of the tile adhesive, and other key properties. For large-scale construction projects, small-scale trials may also be considered to verify the suitability of the formula and process. After the construction is completed, regular inspections should be carried out to ensure that the tiles are bonded well and that there are no problems such as falling off or cracking.
Conclusion
As an important additive, RDP plays a key role in the application of tile adhesives. By rationally designing the formula, controlling the construction process, and properly handling the construction environment, the viscosity-increasing, flexible, and water-resistant properties of RDP can be fully utilized to ensure the bonding effect and service life of the tile adhesive. However, the application effect of RDP is affected by many factors, and it is necessary to continuously accumulate experience in practice and optimize the process flow to achieve the best use effect. In future research and applications, the application of RDP in tile adhesives will continue to expand and become an important part of the field of building materials.
With extensive experience in the chemical and construction coating and tile industry, Mikem has established expertise and credibility to meet our customers' requirements and exceed their expectations. HPMC, HEMC, HEC, and RDP are our core business. We are committed to providing customers with first-class product quality and service. So if you have any questions or needs about RDP or any other related products, please feel free to contact us at any time.
Leave a Reply