
Hydroxypropyl Methyl Cellulose (HPMC) is a cellulose derivative that has become a staple across multiple industries, from construction and pharmaceuticals to food and personal care. Its versatility is due to its unique properties, including water retention, film formation, thickening, and emulsifying abilities. However, HPMC products are not one-size-fits-all; they come in a range of grades, each tailored to specific applications. To make informed decisions in product formulation, it’s essential to understand these grades and their respective uses. In this article, we’ll examine the different HPMC grades and how they’re utilized across various industries.
What is HPMC?
HPMC, short for Hydroxypropyl Methyl Cellulose, is a synthetic polymer that originates from natural cellulose, a key structural element in plant cell walls. The process of creating HPMC involves chemically modifying cellulose through steps such as alkalization, etherification, and neutralization. This results in a water-soluble, non-ionic cellulose ether that boasts various functional properties depending on its chemical structure.
HPMC is particularly valued for its ability to form gels upon heating, its superior thickening properties, robust water retention, and stability across a wide range of pH environments. These features make it an indispensable ingredient in products where controlled viscosity, stability, and texture are crucial.
Differentiating HPMC Grades
HPMC grades are primarily differentiated based on three main factors: viscosity, degree of substitution, and particle size. Each of these factors affects how HPMC behaves in different formulations, thus influencing its suitability for various applications.
Viscosity Grades
Viscosity is a fundamental characteristic of HPMC that significantly influences its performance in various applications. The viscosity of HPMC is typically measured in aqueous solutions under controlled conditions, including specific concentrations and temperatures. It can range from low to medium and high, with each viscosity level tailored for different uses across industries.
Low Viscosity
Properties
Low viscosity HPMC is characterized by its relatively low thickness or resistance to flow when dissolved in water. Unlike higher viscosity grades, low viscosity HPMC creates solutions that are more fluid and easier to pour, ensuring its suitability for applications where a smooth and pourable consistency is essential.
Applications
In the pharmaceutical industry, low-viscosity HPMC is commonly used in tablet coatings and capsule formulations. Its main role in these applications is to form a protective film around the tablet or capsule, enhancing stability, controlling the release of active ingredients, and improving the product's overall appearance. The low viscosity ensures that the coating solution remains thin and easy to apply, facilitating efficient processing during manufacturing.
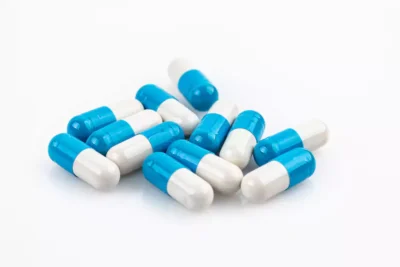
HPMC use for capsule coatings
In the food industry, low-viscosity HPMC acts as an effective stabilizer and emulsifier. It helps maintain uniform texture and consistency in products like sauces, dressings, and beverages by preventing ingredient separation, resulting in a smooth, appealing final product. Additionally, low-viscosity HPMC is often used in dairy alternatives and gluten-free products to replicate the texture of traditional dairy or gluten-containing foods.
Medium Viscosity
Properties
Medium viscosity HPMC is a grade of HPMC that strikes a balance between fluidity and thickness. It offers a moderate level of viscosity, making it suitable for applications that require a balance of flow properties and thickening effects.
Applications
In the construction industry, medium viscosity HPMC is a vital component in tile adhesives, cement-based plasters, and mortars. Its medium viscosity enhances the workability of these materials, making them easier to spread and apply. Additionally, it improves water retention, which is essential for preventing premature drying and cracking, ensuring a durable, long-lasting finish.
In personal care products, medium viscosity HPMC is used in formulations such as shampoos, lotions, and creams. It helps achieve the desired texture, making these products smoother to apply and spread on the skin or hair. Furthermore, it stabilizes the formulation by preventing ingredient separation, ensuring consistent product quality throughout its shelf life.
High Viscosity
Properties
High viscosity HPMC is a grade of HPMC that offers significant thickening properties and is characterized by its high resistance to flow when dissolved in water. This makes it particularly useful in applications where substantial body and structure are required.
Applications
In the construction industry, high-viscosity HPMC is commonly used in products like exterior wall putty, joint fillers, and self-leveling compounds. Its thickening capabilities offer superior adhesion and improved workability, ensuring that the material stays securely in place during application and remains workable for a longer duration. This quality is particularly valuable in construction, where materials need to be easily adjusted to achieve a smooth, even finish.
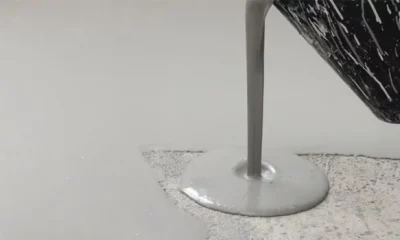
HPMC for self-leveling compounds
In the pharmaceutical industry, high-viscosity HPMC is critical for controlled-release drug formulations. These formulations are designed to release the active ingredient gradually over an extended period, providing sustained therapeutic benefits and enhancing patient adherence. The high viscosity HPMC creates a gel matrix that regulates the drug's release rate, allowing for precise control over the release profile.
Degree of Substitution Grades
The degree of substitution (DS) refers to the extent to which the hydroxyl groups in the cellulose molecule are replaced by methoxyl and hydroxypropyl groups. This chemical modification impacts the solubility, gelation temperature, and overall performance of HPMC in various formulations.
High Methoxyl Content
Properties
HPMC with a high methoxyl content possesses distinct characteristics. The high methoxyl content lowers the gelation temperature, meaning the material forms a gel at a relatively lower temperature compared to other grades. Additionally, high methoxyl HPMC is more soluble in cold water, allowing it to dissolve easily and rapidly, which is advantageous in formulations that require fast dispersion and hydration. This grade also exhibits excellent water retention, helping to maintain moisture in products.
Applications
In the construction industry due to its unique properties, it is commonly utilized in applications such as tile adhesives, cement-based plasters, and mortars. High methoxyl HPMC offers excellent water retention, which is crucial for preventing premature drying and improving the curing process of cementitious materials. This results in stronger adhesion and enhanced durability of the finished product. Additionally, high methoxyl HPMC improves the workability of these materials, making them easier to mix, spread, and apply. It ensures a smooth, even application and reduces the risk of cracks and surface defects.
In the pharmaceutical industry, high methoxyl HPMC is used in fast-dissolving coatings for tablets and capsules. These coatings dissolve quickly in the gastrointestinal tract, allowing for the rapid release of the active ingredient. This is particularly useful in formulations designed for immediate relief or fast action.
In the food industry, high methoxyl HPMC is often used in instant food products. For example, in powdered soups or instant puddings, this grade of HPMC quickly dissolves in water or milk, providing the desired thickness and consistency within minutes.
High Hydroxypropyl Content
Properties
One of the key characteristics of high hydroxypropyl content HPMC is its improved thermal stability. It can withstand higher temperatures without degrading, making it suitable for use in environments where heat resistance is important. This grade also provides better flexibility and film-forming ability, which is particularly beneficial in coatings and films where a flexible, durable layer is needed. Additionally, high hydroxypropyl content HPMC offers enhanced lubricity, improving the workability of mixtures and reducing friction during processing.
Applications
In the construction industry, high hydroxypropyl HPMC is commonly used in thermal insulation mortars, where it ensures consistent performance even with temperature fluctuations. Its high gelation temperature is particularly beneficial in hot-melt adhesives, allowing the adhesive to remain stable and effective during high-temperature applications.
In the food industry, high hydroxypropyl HPMC is incorporated into products such as pie fillings and custards that are cooked or baked. Its excellent thermal stability helps these products maintain their structure and consistency, even when exposed to the heat of cooking or baking.
Particle Size Grades
Particle size is another crucial factor that influences the performance of HPMC in various applications. It affects the dispersibility and dissolution rate of HPMC in water, which are critical for achieving a uniform mixture in different formulations.
Fine Particle Size
Properties
HPMC with a fine particle size offers several key properties that enhance its performance in various applications. The increased surface area of fine particles leads to faster dissolution in water, providing more homogeneous solutions and improved dispersion. This results in better thickening efficiency and rheology control, particularly in formulations like wall putty, where it contributes to smoother finishes and improved adhesion. Additionally, fine particle HPMC enhances water retention.
Applications
This makes fine particle size HPMC ideal for applications in paints and coatings, and cosmetic formulations. In paint and coating formulations, fine particle size HPMC improves the viscosity and flow of the product, ensuring an even application without streaks or clumps. Fine particle HPMC enhances water retention, which is crucial for cement-based systems, and promotes better film formation in coatings, leading to enhanced durability and flexibility. However, it's important to note that while these finer particles improve performance, they may also reduce the flowability of the powder during processing.
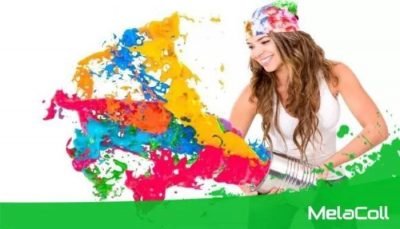
HPMC for coating and paints
In cosmetics, such as foundations and creams, fine particle size HPMC helps create a smooth texture, enhancing the product's feel and appearance on the skin.
Coarse Particle Size
Properties
HPMC with a coarse particle size exhibits properties that can influence its application differently compared to finer particles. Coarse particles generally have a slower dissolution rate, which can be advantageous in processes where controlled or delayed hydration is desired. They tend to flow better as a dry powder, making them easier to handle and process in large-scale manufacturing. However, their lower surface area may lead to less efficient thickening and water retention compared to finer particles.
Applications
In the construction industry, coarse particle size HPMC is used in plasters, renders, and self-leveling compounds. The slow dissolution rate helps maintain the workability of these materials over an extended period, allowing for more time to apply and finish the product. This is particularly useful in large-scale construction projects, where the material needs to remain workable for long periods.
In the pharmaceutical industry, coarse HPMC particles are used in sustained-release formulations, where the goal is to gradually release the active ingredient over several hours, ensuring consistent therapeutic effects without the need for frequent dosing.
Conclusion & MIKEM
Understanding these factors—viscosity, degree of substitution, and particle size—allows manufacturers to select the appropriate HPMC grade for their specific application needs, ensuring optimal performance and product quality.
MIKEM is a global manufacturer and supplier of specialty chemical products. Headquartered in Dallas, USA, we have branches, offices, manufacturing plants, sourcing teams, and warehouses in different countries. Cellulose ether is MIKEM’s core business and most competitive product line. We are honored to provide you with high-quality Melacoll® HPMC, HEMC, and HEC. Welcome to contact us for your business needs at any time!
Leave a Reply