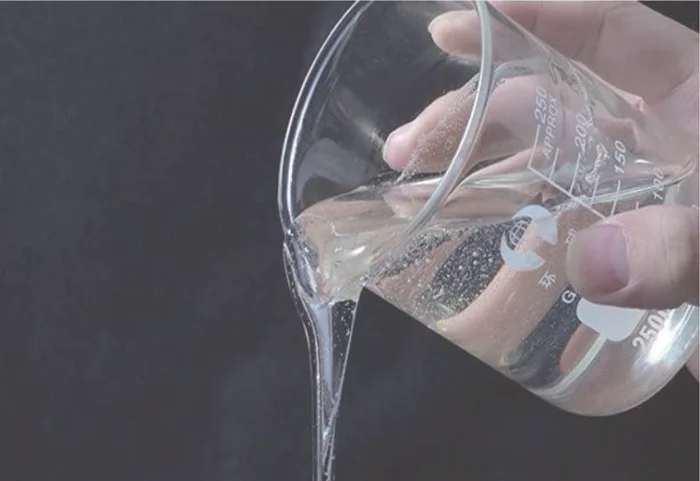
HPMC is a very popular cellulose ether that plays an important role in the fields of construction, pharmaceuticals, daily chemicals, food, etc. So how to make HPMC powder? The basic steps are: raw material preparation, alkali treatment, etherification, methylation, hydroxypropylation, and purification and drying.
Raw Material Preparation
The production of Hydroxypropyl Methylcellulose (HPMC) powder starts with cellulose as the base material. Common sources are wood pulp and cotton linters. Wood pulp, being cost - effective, is first processed to remove lignin and other non -cellulose components. Cotton linters, having a high cellulose content, so using refined cotton as raw materials to produce HPMC viscosity will be higher.
Alkali Treatment
The selected cellulose is treated with an alkali, usually sodium hydroxide (NaOH). This treatment serves two main purposes. First, it causes the cellulose fibers to swell. As the cellulose absorbs the alkali solution, the internal hydrogen bonds within the cellulose structure are disrupted. This physical swelling allows better penetration of subsequent reactants. Second, it activates the cellulose chemically. The hydroxyl groups (-OH) on the cellulose become more reactive, which is crucial for the next stage of the process.
Etherification
Etherification is the core step in making HPMC. Two key reagents are used: methyl chloride (CH₃Cl) and propylene oxide (C₃H₆O).
Methylation
Methyl chloride reacts with the activated cellulose in a nucleophilic substitution reaction. The chlorine atom in methyl chloride is replaced by a methyl group (-CH₃) on the hydroxyl groups of cellulose. This methylation step influences the solubility and hydrophobic nature of the final product.
Hydroxypropylation
Propylene oxide reacts with the remaining hydroxyl groups on the cellulose. The epoxide ring of propylene oxide opens, and a hydroxypropyl group (-CH₂CH(OH)CH₃) attaches to the cellulose. This imparts water - solubility and other useful properties to the HPMC. The reaction occurs in a reaction vessel, with temperature typically maintained between 50 - 100°C and pressure adjusted according to the reaction requirements. The reaction time is several hours to ensure proper substitution.
Purification and Drying
After the etherification reaction, the mixture contains unreacted chemicals, by - products and salts along with the crude HPMC. It is washed with water or a suitable solvent to remove these impurities and then neutralized. The washed HPMC is separated from the liquid phase, for example, by filtration or centrifugation. Finally, it is dried, often through spray - drying. In spray - drying, the wet HPMC is turned into small droplets and dried using hot air, resulting in a fine powder with a uniform particle size.
Summary
The production and manufacturing of HPMC requires certain conditions. Small workshops with relevant equipment can also produce it, but the quality cannot be guaranteed. To find high-quality HPMC powder, you still need the support of regular HPMC manufacturers!
Leave a Reply