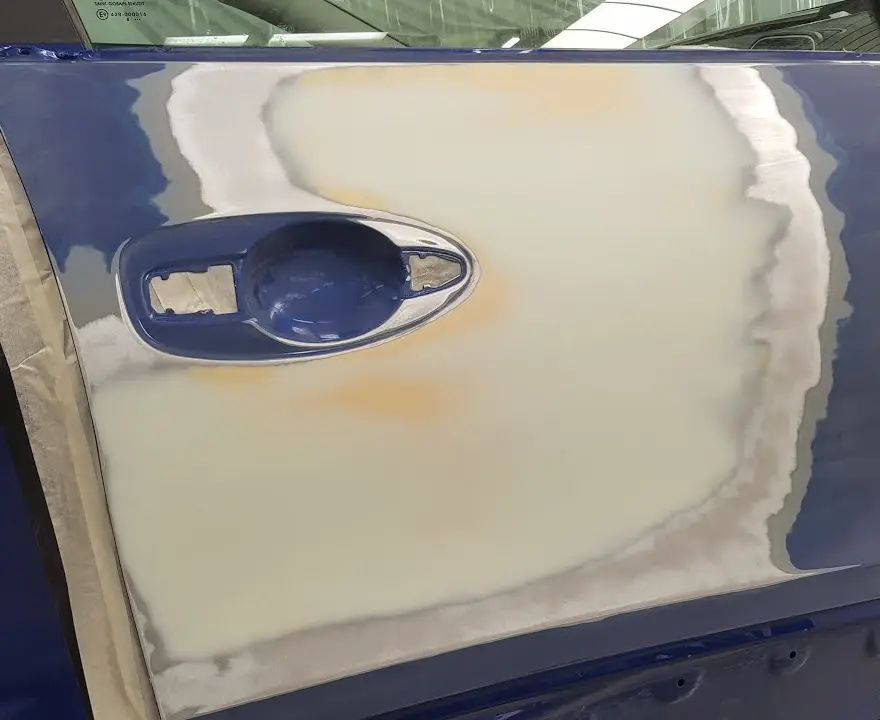
Polyester Putty is a two-component filler repair material based on unsaturated polyester resin, which is widely used in the fields of automotive repair, shipbuilding, furniture refinishing and architectural decoration due to its fast curing speed, strong adhesion and excellent shrinkage resistance. Its core value is to quickly fill the defects of the substrate and form a high-strength surface layer, providing a flat substrate for subsequent painting processes.
Polyester Putty Formulation Core Ingredient Analysis
Main resin system
Unsaturated polyester resin (40-60%)
As the main film-forming substance, o-phenylene or m-phenylene resins are usually used to provide basic adhesion and mechanical strength. Vinyl ester resins are added to high-end formulations to improve corrosion resistance.
Curing Systems
Peroxide initiator (1-3%)
Methyl ethyl ketone peroxide (MEKP) is commonly used as a curing agent, which reacts with the styrene monomer in the resin in a free radical polymerization reaction. It needs to be added in strict proportion, and excessive amount will lead to embrittlement.
Cobalt salt accelerator (0.2-0.5%)
Cobalt naphthenate or cobalt octanoate can accelerate the curing reaction, and need to be increased appropriately in winter construction.
Filling Reinforcement System
inorganic filler(35-50%)
Packing type | particle size(μm) | primary role |
talc | 5-20 | Improve sandability and reduce costs |
calcium carbonate | 10-30 | Increase volume stability |
glass beads | 50-100 | Reduced density, anti-settling |
silica micropowder | 3-10 | Improved hardness and wear resistance |
Functional additives
Thixotropic agent (0.5-1.5%)
Hydrogenated castor oil or fumed silica imparts thixotropic properties to the system and prevents sagging on vertical surfaces.
Pigments (1-3%)
Iron oxide red/yellow to provide workability, titanium dioxide for light-colored formulations.
Defoamer (0.1-0.3%)
Polyether-modified silicone eliminates air bubbles from mixing.
The standard construction process
Substrate pretreatment
The metal surface needs to reach Sa2.5 level sandblasting treatment, wood moisture content control in 8-12%
Cross sanding with 120# sandpaper to increase the mechanical bite
Solvent wipe to remove grease (recommended use of butanone or acetone)
Material mixing
Mix the main agent and curing agent in the ratio of 100:1.5-3 (temperature compensation adjustment)
Stirring time control within 2 minutes until the color is uniform
Applicable period: about 5-8 minutes at 25℃.
Scraping operation
The thickness of the first layer should not be more than 3mm, adopting “cross-batch scraping method”.
The interval time of each layer is 20-30 minutes (after the surface drying construction)
The final thickness is recommended to be ≤5mm, too thick to produce internal stress cracks.
Curing control
Full curing at room temperature (25℃) takes 2-3 hours.
Infrared heating (60℃) can be shortened to 40 minutes.
Curing degree test: use fingernail scratch method to judge the hardness.
Surface Finishing
Use 80#-240# water sandpaper for graded sanding.
The surface roughness Ra≤10μm after grinding is qualified.
After dusting, the primer construction should be carried out within 24 hours.
Control of key technical parameters
norm | Test Standards | Scope of Compliance |
tensile strength | GB/T 1040 | ≥12MPa |
shrinkage | ASTM D2566 | ≤0.5% |
sandability | manual test | No sandpaper sticking phenomenon |
VOC content | HJ 2537-2014 | ≤350g/L |
Solutions to Common Problems
Abnormal curing
Non-curing: check whether the accelerator is invalid, dehumidification is required when the ambient humidity is over 85%.
Localized soft spots: due to uneven mixing, prolong the mixing time.
Surface defects
Pinhole: Add 0.2% BYK-066N defoamer.
Orange peel: Adjust the proportion of thixotropic agent to 1.2%.
Insufficient adhesion
Epoxy transition layer treatment (recommended E-44 epoxy + 650 polyamide)
Safety norms and environmental protection requirements
Forced ventilation in the operation area, VOC concentration <100mg/m³.
Operators must wear 3M 6200 gas mask and nitrile gloves.
Waste curing agent is treated according to hazardous waste code HW13.
New water-based polyester putty VOC can be reduced by 70%.
Technology Development Trends
Nano-modification technology: adding 2% nano-SiO₂ to improve impact resistance by 30%.
UV curing system: reduce energy consumption by 60%, suitable for precision electronic packaging
Bio-based resin applications: castor oil-modified polyester accounted for 35% of the total
Through the systematic mastery of the principles of the formula and construction techniques, the repair efficiency can be significantly improved by more than 30% and the rework rate can be reduced to less than 5%. It is recommended to establish a standardized operation manual and regularly conduct infrared spectroscopy (FTIR) to verify the stability of raw materials.
Leave a Reply